How modular house construction influences the construction industry
The module house building has its roots already in the 60s and 70s. At that time, experiments were carried out with skeleton structures that could be optionally installed and removed in room modules. In the context of urban housing shortages, the construction industry is once again increasingly focusing on the vision of a "stackable city". Read here how modular house construction influences production and what advantages the modularization of the construction industry brings.
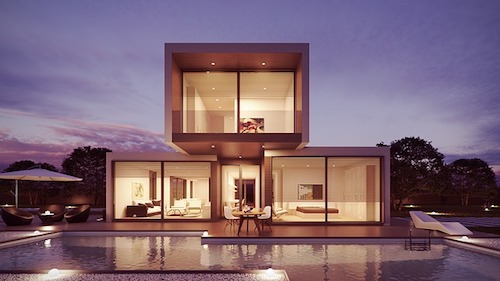
Urbanization as a driver of modular construction
According to the trend radar of the German construction industry, the most important current mega trends for the construction industry are climate change and sustainability, demographic change, digitization, urbanization and infrastructure. Digitization and sustainability are of the highest relevance, but are still relatively rarely used. The trend towards urbanization is also highly relevant, but is already more widespread.
In the field of urbanization, there is also a clear trend towards modular house construction - a construction approach that offers the possibility of creating individual living space more cost and time efficiently. As a result, the modularization of houses within the framework of the trend radar study is also identified as a worthwhile niche for the future.
New concepts through analogies from the automotive industry
The automotive industry has long relied on the advantages of modularization. New concepts in serial and modular construction transfer the principles of modularization in car construction to house construction and manufacture cost-effectively according to individual customer requirements.
1. Prefabricated individual parts
In analogy to car construction, a house is also reduced to a certain number of standard elements (modules) and provided with precisely defined connection points for ceiling, exterior wall or windows. The modules are offered in different versions (variants), just as there are different seats, engines or other equipment for a car. An infinite number of variants of buildings can be assembled from this.
For example, almost 1.7 billion different individual floor plans are already possible for a single-family house with 8 modules and a construction kit with 50 different room modules. Even the most modern technology in terms of energy saving and energy generation can be integrated without any problems.
2. Mass production in the factory
The individual modules are not produced on site, but in the factory. The latest industrial production methods are used, from automation to digitization. Since the modular design allows higher quantities in mass production than in the previous prefabricated house construction, this results in an enormous gain in productivity and thus a considerable reduction in costs. Model calculations show savings of 50 to 75 percent compared to conventional construction methods. In addition, construction projects are completed more than 70 percent faster.
3. Configuration and ordering via PC
In the same way that you put together your dream car using a configurator today, a customer can also create his future home on the computer. This has two major advantages: On the one hand, the customer can change the plan as often as he wants without additional costs, on the other hand, data is generated via the configurator, which is available to the architect, the authorities, the production planner in the factory and the fitters on the construction site.
This is why digitization with the Building Information Modeling (BIM) system is becoming increasingly important, particularly in modular construction. Material bills of materials and possible product variants must be preconfigured down to the last detail and be available in production in order to take advantage of the modular design.
© Bausoft Solution, Graz
The BIM also enables the ongoing exchange of information between all parties involved during the construction phase and thus supports the realization of the construction project within the specified time and budget and with a low error rate. Although the BIM is already widely known in the construction industry, there is often still a lack of knowledge to transfer the analog working environment into a digital and networked value-added process.
4. Quick installation
As soon as the foundation and cellar have been completed, only the finished modules have to be installed. Since pipes and cables have already been installed in the factory, nothing needs to be repaired. This enables construction sites to be completed faster and more efficiently. The greatest savings are therefore achieved on the construction site, since 80 percent of the added value in modular house construction already takes place in upstream process steps in the factory.
Advantages of the modular design
The concept of modularization solves the conflicting goals of the construction industry of being able to offer products that can be customized while at the same time being cost efficient. In terms of cost-effectiveness, this results in advantages over conventional construction methods in terms of cost, time, quality assurance and flexibility.
- Higher cost efficiency: Industrial prefabrication enables customer-specific construction projects, which account for less than half of the production costs compared to conventional construction site production. The cost reductions also result from the direct integration of customers into the value chain and from the modularization of product and production.
- Reduced planning costs: By reusing modules once planned, planning costs incurred by highly qualified personnel can be reduced.
- Lower material and logistics costs: In production, the bundled procurement of building materials realizes purchasing advantages and thus saves further costs.
- Savings through customer preferences: Further savings potential results from the fact that for most customers the internal flexibility of the house is more important than the exterior. This means that parts from the outside can be standardized rather than parts from the inside.
- Lower investment and maintenance costs: Both investment costs for machines and systems and maintenance costs are reduced in modular production.
- Increased productivity: The use of largely standardized components enables the acceleration of product and production start-ups as well as the increased use of robots.
- Quality assurance: Modular house construction scores particularly highly in quality assurance in production and on the construction site. The use of market-ready and proven modules increases the quality of the production processes and at the same time reduces the susceptibility to errors. In addition, a comprehensive, integrative design avoids errors that occur in conventional house construction by coordinating the various trades at different times and locations.
- Time savings: Prefabrication allows construction sites to be completed faster and more efficiently. In addition, the dependence on the weather decreases. This makes construction time easier to plan and shorter overall.
- Flexibility: The products are optimally scalable due to the modular production and can be flexibly adapted to the needs of the customers.
- Gaining market share: The combination of individually scalable houses at favorable conditions provides modular house construction with a product attractiveness that allows it to gain additional market share.
Conclusion: Modular house construction as a promising niche
Modular house construction offers the possibility to realize individual building projects at lower costs and with less time. In this way, modularization can make an important contribution to counteracting the housing shortage in urban regions.